Key Tactics for Sustainable Hiring in Additive Manufacturing
March 19, 2024
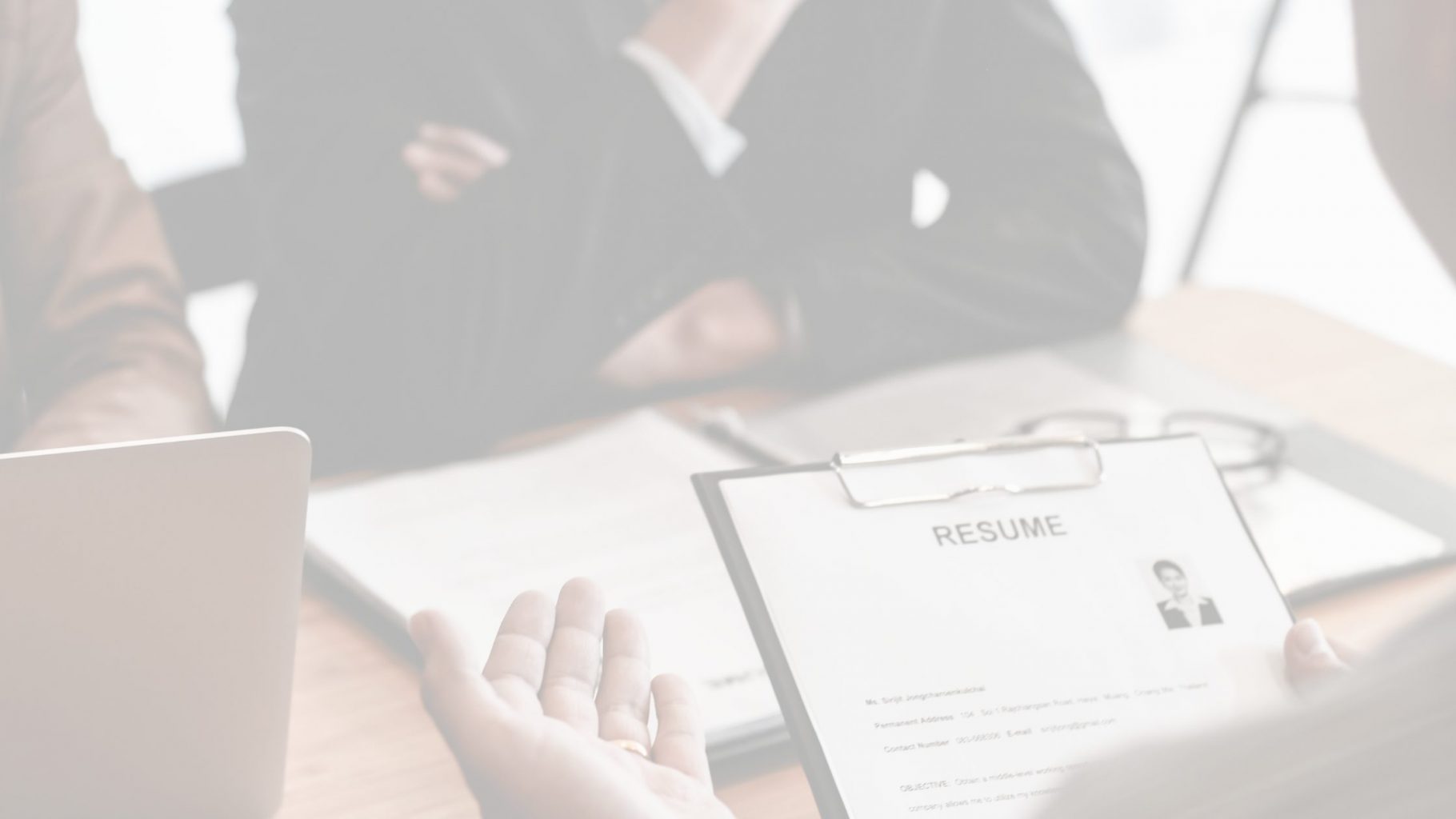
When a pivotal role remains unfilled within the additive and advanced manufacturing industries, the repercussions can reverberate throughout a company. The impact of an empty position is significant, from financial strains due to lost revenue and increased overtime to a decrease in staff morale and potential mistakes from overworked employees.
Delayed projects, different account managers affecting customer satisfaction, and the risk of panic hiring leading to a further turnover cascade highlight the criticality of timely recruitment.
In this blog, we will explore the business implications of vacancies, explore strategies to mitigate their effects, such as cross-skilling, succession planning, and strategic recruitment initiatives, and examine the long-term benefits of sustainable hiring practices to ensure operational continuity and growth within the additive manufacturing sector.
The Impact of an Empty Role on Business
Detriments of Unfilled Positions
An empty position within a company can act like a gear missing in a complex machine, disrupting the entire operation. Financially, the absence can mean lost revenue and increased overtime costs as other staff members try to fill the gap. This strains budgets and can lead to burnout among team members, shouldering extra work, resulting in lower productivity and possibly more errors due to fatigue.
Staff morale may suffer as the workload imbalance can create a stressful work environment. This stress can then affect customer service, as overburdened employees are less likely to provide the high-quality interaction and attentiveness customers expect.
In the additive manufacturing sector, where precision and reliability are paramount, these detriments can undermine a company’s reputation for quality and reliability, potentially losing trust from clients and partners.
The Domino Effect of Panic Hiring
In the rush to fill a crucial role, companies may resort to panic hiring, a short-sighted solution that often exacerbates the problem. Panic hiring typically involves making a quick decision without thorough vetting, which can lead to a poor fit between the new employee and the company. This misalignment can result in decreased productivity and often lead to the new hire leaving prematurely, restarting the costly recruitment cycle. Additionally, the rest of the team may suffer from the disruption of repeatedly adjusting to new members who may not stay long-term.
In the additive manufacturing industry, where projects require a deep understanding of complex processes, the consequences of such turnover can be particularly severe, leading to project delays and compromised quality. Therefore, resisting the temptation to make hasty hiring decisions that can trigger a domino effect of ongoing staffing issues is essential.
Approaches to Mitigating the Impact of an Empty Role
Understanding the Root Causes of Job Vacancies
Identifying the underlying reasons for job vacancies is critical to developing effective strategies for sustainable hiring. Often, vacancies arise not just from employees leaving but also from growth and structural changes within a company. In the additive manufacturing sector, rapid technological advancements can create new positions faster than they can be filled, leaving gaps in the workforce.
Other times, a mismatch between the skills sought after and those available in the job market can lead to prolonged job openings. Additionally, a company’s reputation, location, and the perceived attractiveness of the role can significantly affect the ability to attract suitable candidates.
By understanding these root causes, businesses can tailor their recruitment efforts to address these specific challenges, making the hiring process more efficient and reducing the likelihood of future vacancies. This approach ensures a more stable workforce and continuity in business operations.
Cross-Skilling and Interim Employment as Short-term Solutions
Cross-skilling existing employees is a viable short-term solution to bridge the gap created by job vacancies. Companies can maintain productivity levels by training staff to handle multiple roles even when key positions are unfilled. This approach provides immediate relief and empowers employees with new skills, boosting morale and career development. It also fosters a flexible and adaptable workforce that can pivot according to business needs.
Interim employment is another strategy, where temporary workers are brought in to fulfill duties while the search for a permanent employee continues. This can be particularly useful in the additive manufacturing industry, where the skill sets required are highly specialized. Interim professionals can keep projects moving forward without the commitment of a permanent hire, providing a buffer period to find the right candidate without rushing the decision. Both cross-skilling and interim employment can serve as effective stopgaps, preventing the costly effects of hasty hiring decisions.
The Importance of Succession Planning
Succession planning is a strategic approach to ensure business continuity and prevent the negative impact of unexpected vacancies. By identifying and developing internal talent for future leadership roles, companies can create a pool of qualified candidates ready to step in when senior positions become available. This proactive process eliminates the rush to find external candidates and reduces the time positions remain vacant.
In the additive manufacturing industry, where specialized knowledge is critical, internal candidates already familiar with the company’s processes and culture can transition into new roles more smoothly. Succession planning also signals to employees that there are opportunities for growth within the company, which can enhance staff retention and engagement. When implemented effectively, it allows for a more seamless changeover in leadership, minimizing the risk of disruption to the company’s operations and maintaining momentum in business activities.
Timing and Preparation – Recruitment for Planned Vacancies
Effective recruitment requires foresight and preparation, especially with planned vacancies. Anticipating the need for new talent and starting the recruitment process early can prevent a rushed hire and ensure a better fit. In additive manufacturing, where roles often require a high degree of technical expertise, finding the right candidate can take time. Early planning allows for a broader search and a more thorough evaluation of potential hires.
Timing also plays a crucial role. By aligning recruitment efforts with industry cycles and business seasons, companies can avoid peak times when competition for top talent is fiercest. This strategic timing also helps businesses to onboard new employees during slower periods, allowing for smoother integration into the team without the pressure of immediate high-stakes projects. Preparation and timing in recruitment fill vacancies more effectively and build a stable foundation for future growth.
Remembering the Time Factors – Employee Notice Periods
It’s crucial to account for new employees’ notice periods. These time frames can substantially impact how quickly a role can be refilled. In the advanced manufacturing industry, where specialized skill sets are often required, notice periods can extend even longer, making the anticipation of departures even more critical.
Companies should be aware of typical notice periods, which allows them to initiate the recruitment process well in advance. Building this time into the process ensures a buffer period for finding and training a replacement without a lapse in productivity.
Key Takeaways
In additive manufacturing, the absence of a key player can send ripples throughout the business ecosystem. The impacts are far-reaching, from financial strains to a decline in team morale. Panic hiring, a reaction to such pressures, can compound the problem, leading to a vicious cycle of high turnover and missed opportunities.
Sustainable hiring strategies are the antidote to these challenges. By understanding the underlying causes of vacancies, companies can tailor their recruitment processes for better outcomes. Short-term solutions like cross-skilling existing employees and leveraging interim employment can help bridge the gap while the right candidate is found. Succession planning provides a forward-thinking strategy for business continuity and growth by fostering internal talent.
Effective recruitment for planned vacancies requires early action, strategic timing, and preparation, ensuring a wider pool of potential hires without the rush. In an industry where precision and expertise are paramount, such strategic moves become instrumental in maintaining operational fluidity.
In short, a well-thought-out approach to recruitment can save additive manufacturing companies from the detrimental effects of unfilled positions. By focusing on sustainable hiring practices, businesses can ensure their present operational continuity and lay the groundwork for future growth and success.
Related news
Join our newsletter
Sign up to discover the latest jobs, market insights, blogs and more
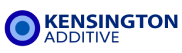
All content copyrighted Kensington Additive © All rights reserved