ADDITIVE MANUFACTURING: WHO'S IN THE NEWS? #1
March 15, 2021
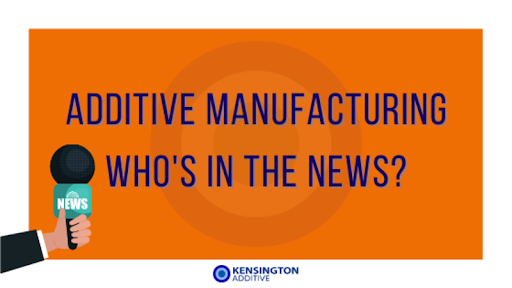
Every day we’re witness to updates and announcements in the 3D Printing industry. Kensington Additive has decided to offer a fortnightly news-round up in blog form, to keep our network informed of all the goings on. By sharing all the latest headlines and articles from 3D Printing’s media outlets, we’re aiming to inform our audience on a regular basis.
Let’s see who’s in the news…
- Wayland Additive, a Yorkshire based company who exist to make electron beam additive manufacturing more effective and accessible to the industry, has launched it’s Calibur3 metal additive manufacturing system.
The system is powered by NeuBeam technology, which is a powder bed fusion process. The benefits of this is that the system is capable of processing a wide range of metal materials and can product large parts without residual stress or gas cross flow. The company is aiming to host a physical launch event in May.
Read more on the TCT website
- Markforged, the U.S. manufacturer of metal and composite 3D printers, has launched the new AI-based Blacksmith software for use with the X7 3D printer.
Blacksmith can accurately measure the dimensional precision of parts as they are being printed, and then the scan data is cross-references against the intended design giles. This offers manufacturers the ability to assess how close the printed part is to the original STL, meaning that in future the reliability process can be improved.
Read more on the 3D Printing Industry website
- VELO3Dis a leader in the evolution from the analog supply chain to digital manufacturing, and now a huge milestone has been reached, as it’s set to become a public company.
The company’s proprietary full-stack 3D metal printing solution enables the production of mission-critical components for space rockets, jet engines, fuel delivery systems and energy production with better performance, at faster speed and lower cost than traditional methods.
VELO3D’s founder and CEO Benny Buller and CFO William McCombe, will continue to lead the Company through its next phase of growth.
- Ford, the world-renowned car manufacturer has partnered with 3D printer OEM HPto recycle 3D printing waste into end-use automotive parts.
What is known to be an industry first, the partners have started converting recycled 3D printing material into injection molded fuel-line clips for use on Ford’s Super Duty F-250 trucks. The parts supposedly offer better chemical and moisture resistance in comparison to conventional counterparts with fresh materials, and are even 7% lighter and 10% cheaper to produce.
Read more on the 3D Printing Industry website
- International personal care brand L’Oréalhas adopted AMFG’s Manufacturing Execution System (MES) software, in order to optimise the company’s rapid prototyping workflows.
L’Oréal is said to produce thousands of 3D printed prototypes every year at its 3D Lab in Clichy, France and has invested in AMFG’s MES platform to support the increasing volumes with which it is printing at.
Read the full article on TCT’s website
- Ever seen a filament made from wine?
Coffee grounds, hemp and food waste have been used to make filaments, mainly to address sustainability in the 3d printing industry, but now added to this list is wine.
An American Start-Up, Wine Not, which is using wine waste, known as grape marc or pomace, as a base for its thermoplastic filaments intended for use in 3D printing.
Read more on the 3Dnatives website
- Mighty Buildings, a California-based construction technology company, has announced plans to build 15 homes using prefabricated 3D printed panels in Rancho Mirage, California.
The project is a collaboration between Mighty Buildings and developers Palari Group. When complete, Mighty Buildings claim that the development will be the “world’s first community” of 3D printed homes with net-zero emissions.
Solar panels will provide energy for the properties and individual houses will also have the option to use Tesla Powerwall batteries to store the solar energy.
Read more on the Dezeen website
- A UK-based manufacturer of low-pressure air ducting and air handling systems for aerospace, Senior Aerospace BWT, has grown its production capacity with the installation of 3D printers for the additive manufacturing of thermoplastic aircraft interior parts.
The company says that the 3D printing technologies yield “significant savings” in terms of component weight, cost and lead-time, compared with the use of aluminium. For certain parts, Senior Aerospace BWT claims savings of as much as 75% – particularly for small order quantities.
Read more on Aircraft Interiors International’s website
And that wraps up the first Who’s in the News blog. Stay tuned for the next blog in two weeks or sign-up to our marketing emails, to remain in-the-know.
Related news
Join our newsletter
Sign up to discover the latest jobs, market insights, blogs and more
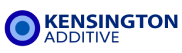
All content copyrighted Kensington Additive © All rights reserved